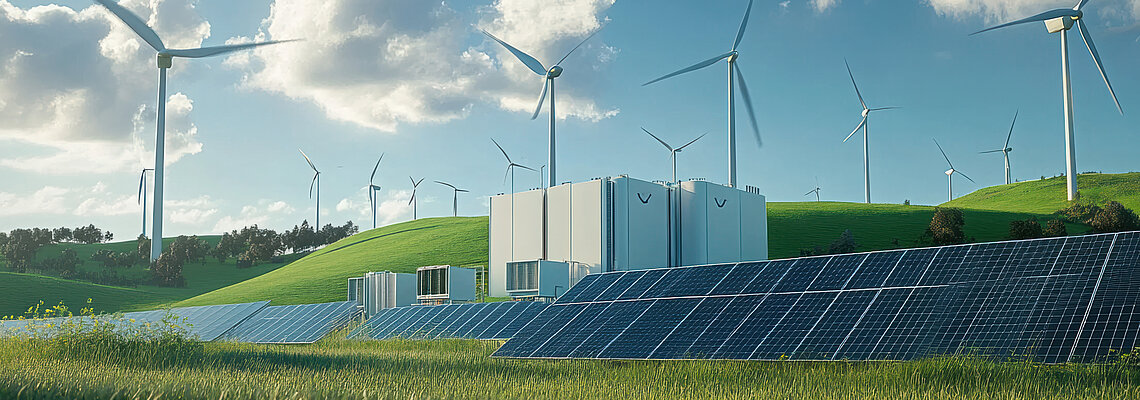
Minimize Downtime in Battery Energy Storage Systems by Locating Ground Faults Quickly
The world’s energy landscape is rapidly evolving. With the increasing demand for reliable and clean energy sources, the integration of smart grids, photovoltaic systems, and battery energy storage systems (BESS) have become essential. As these systems grow in scale and complexity, ensuring the safety of both personnel and equipment has never been more critical.
One of the most common challenges faced in battery storage systems is managing ground faults - issues that can result in downtime, equipment damage, and safety risks. However, by leveraging the latest monitoring technology, these faults can be detected and addressed quickly, minimizing downtime and ensuring the long-term reliability of BESS.
Understanding Ground Faults in Battery Energy Storage Systems
Battery energy storage systems most often operate as ungrounded systems, where every current carrying conductor is intentionally isolated from the ground. This setup allows the system to continue operating even if a single ground fault occurs. However, while these systems are designed to tolerate a single fault without shutting down or creating a significant shock risk, it is crucial to identify and clear the first fault as quickly as possible. If a second fault occurs before the first is addressed, a dangerous line-to-line short circuit could occur, creating hazardous overcurrent conditions that may damage equipment, lead to fires, or endanger personnel. In outdoor systems, multiple lines are likely to age and degrade at similar rates due to weather, condensation, or UV exposure; so, two faults occurring in relatively short succession is not unlikely. Large BESS installations can make locating the cause of a ground fault difficult and time consuming
This is where real-time monitoring and fault detection technology becomes essential. By rapidly detecting ground faults and accurately locating them, operators can easily locate, isolate, and correct faults to prevent catastrophic failures, maintain the continuity of service, and ensure safety in BESS installations.
The Role of Bender Monitoring Equipment
Bender monitoring equipment offers state-of-the-art technology designed to quickly and accurately detect ground faults and other insulation breakdown issues in battery storage systems of virtually all sizes. With robust communication options, including Ethernet and Modbus, Bender systems can be seamlessly integrated into industrial networks, allowing for efficient monitoring and rapid responses to emerging issues. The data can also be tracked over time to gauge overall installation health trends, plan preventative maintenance, or provide other insights into system behavior.
🎥 Watch Bender technology in action
Here are a few key ways Bender technology enhances the efficiency and safety of BESS:
1. Detecting Faults Without Interrupting Operations
A key benefit of Bender monitoring systems is their ability to detect ground faults without interrupting system operation. This is especially critical in energy storage systems, where continuity of service is essential. The system can identify faults or insulation breakdowns while keeping the installation energized.
The Bender insulation monitoring device (iso685-D-P) and earth detection system (EDS 44x series) work together to aid in accomplishing this. Our iso685-D-P provides that active, real-time measurements, and when insulation values drop below the user-configurable threshold, the EDS44x activates and begins locating the fault. This means that operators can take corrective actions without the need for expensive downtime while searching and troubleshooting the system, which is a significant advantage in any high-demand energy environment.
2. Reducing Maintenance Costs
A well-designed fault detection system also helps reduce maintenance costs. Traditional fault detection methods often require significant human interaction with the system, including manual checks and inspections, often requiring significant PPE (personal protective equipment) when working on an energized system. With accurate and automated fault location systems from Bender, the need for frequent, labor-intensive maintenance is greatly reduced. Automated alerts and diagnostics mean that technicians only need to focus on confirmed issues, preventing unnecessary visits to the installation site. This streamlined approach to maintenance saves time, reduces operational costs, and increases the overall lifespan of the system.
3. Automatic Fault Location
A ground fault is a serious concern, and timely action is needed to prevent further damage. Bender systems that include an EDS440 earth detection system, automatically locate faults in real time, eliminating the need to open branch circuit breakers or disconnect critical equipment. The technology pinpoints the precise location of the fault, so operators can act swiftly and with confidence. This eliminates uncertainty and ensures that repairs can be conducted as quickly as possible.
4. Enhanced Safety for Personnel
Safety is a top priority in any energy storage environment. By accurately locating faults at feeders and loads, the system minimizes the risk of electric shock, equipment damage, and other hazards. Quick identification of the fault means that repairs can be performed faster, reducing the risk of fire or other catastrophic events. With built-in real-time alerts and diagnostic information, safety teams can quickly assess the situation and respond appropriately, ensuring the well-being of employees and minimizing damage to the equipment.
5. Monitoring and Prolonging System Life
Monitoring and storing system history can enable additional insights by operators, such as observing seasonal or weather-related effects on the insulation of the system. By storing and analyzing this data, operators can better differentiate system component degradation from normal operating conditions and plan appropriate preventative maintenance measures. By detecting faults early and resolving them before they cause larger issues, Bender systems contribute to the long-term health of the battery energy storage system. Addressing faults quickly helps avoid scenarios that could result in overcurrent conditions, overheating, or component failures. As a result, the life cycle of the entire system is extended, leading to lower replacement costs and a more efficient energy storage operation.
Conclusion
As the world increasingly turns to renewable energy solutions,battery energy storage systems play an integral role in balancing energy supply and demand. However, ensuring that these systems run safely and efficiently requires addressing the challenges posed by ground faults. By leveraging advanced monitoring technology like Bender systems, operators can detect and locate faults in real time, preventing costly downtime, reducing maintenance costs, and improving safety. The result is a smarter, more reliable BESS, providing a steady and sustainable flow of energy with minimal disruption.
With a reliable fault detection system in place, battery energy storage systems can thrive, meeting the growing energy demands of the future while keeping personnel and equipment safe.
At Bender Inc., we’ve been at the forefront of electrical safety for over 75 years. Our commitment to innovation and excellence drives us to create solutions that exceed expectations. When it comes to protecting your commercial kitchen, trust the experts—trust Bender.
For more information about this application or to learn more about Bender technology related to your specific application, contact our team of experts.
This article is for informational purposes only. Bender provides the information "as is" without warranty and is not responsible for its accuracy or reliability. No warranties are given regarding its suitability for any specific circumstances.