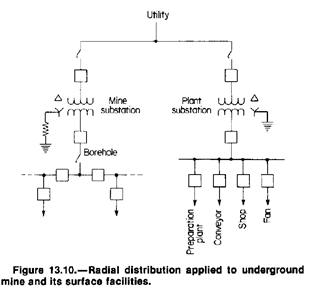
Mining consists of both extraction and processing. North American mine extraction areas have used resistance grounding successfully for a long time. Historically, the plant/processing area of mines has used solidly-grounded distribution of power identical to those used in other commercial and industrial designs. The simple schematic on the right is extracted from an MSHA information Circular 9258 Mine Power Systems By Lloyd A. Morley.
Similar designs are still prevalent today, with solid grounding on the plant side. There can be an improvement in safety and productivity if resistance grounding is adopted throughout the mine. The high-voltage distribution brought in from utility is typically not high-resistance grounded as the voltages are not compatible with continued operation under fault. They must trip on a ground-fault condition as a single phase-to-ground fault could quickly escalate to a phase-to-phase fault. Some customers have used Low Resistance Grounding (LRG) on the incoming high-voltage distribution. It offers some benefits over solid grounding – primarily lower fault current and, therefore, less damage at the point of fault. There is a risk of the system becoming ungrounded if the resistor or its connections between ground and the transformer neutral were to fail. Bender recently launched the NGRM550 and NGRM750 to mitigate the risk and provide protection for LRG systems.
Improvement 1: Implement portable load shock protection with HRG
In many jurisdictions around the globe, extraction areas (both underground and surface operations) are required by law to use high resistance grounding. These systems differ from continuous process areas since they are also required to trip on the occurrence of a ground fault. In some jurisdictions, monitoring the continuity of the grounding resistors is mandatory. Bender NGR monitors for high resistance grounded systems (NGR500, NGR700) have been adopted by many customers. Ground monitors, ground conductor monitors, or ground check relays such as the RC48C are also used to improve safety and help prevent electric shock or electrocution. As you can see by the image below, during a ground fault, there is a potential for current flow through the human.
Tripping on the occurrence of a ground fault limits the probability of an incident. Engineering controls like the protective relays, lower resistance (larger ground wires) to the portable equipment, and restricting ground-fault current with a high resistance grounding resistor (HRG) help control the potential current flow. The probability of human interaction with a fault is minimized because when a fault is detected the contactor or/breaker starts to interrupt the power. It is a common misconception that all HRG systems are alarm only – they are not.
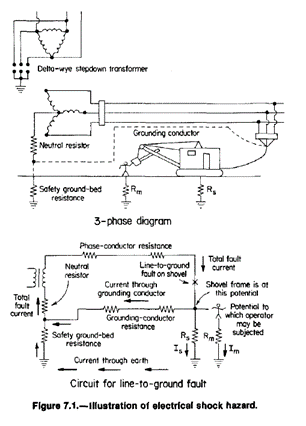
Improvement 2: Utilize Bender HRG and LRG systems to improve safety and limit point of fault damage
The processing area for different types of mines is unique to the product they are selling. They are all similar in that they do not like to have unplanned downtime -just like any industrial facility. Undue stress and costs are associated with after-hour service call-outs and the potential for not meeting delivery commitments. High resistance grounding alarm-only systems are employed at many modern facilities to improve uptime. Continuing to run until the end of a shift, batch, or through the night can help production meet their goals and help maintenance plan for troubleshooting and repair.
Consider the costs of an issue with the ventilation fans on the bottom right of Drawing 1. Diesel- and gas-powered equipment are still prevalent in mining. There are federal requirements for fresh air in underground operations, such as the mines must be evacuated for safety if the fans are not operational. HRG can help them maintain operations during a ground fault. Electric vehicles used underground have helped reduce some of the health risks associated with diesel exhaust and reduce some of the demands for fresh air.
Improvement 3: Consider adding the RCMS490 for automatic fault location
HRG systems also improve safety as there is no arc flash possible from a single phase-to-ground fault. This is a great improvement over the solidly grounded system shown in Drawing 1. It's important to note all AC systems have a risk of phase-to-phase and three phase faults that cause arc flashes – so there is no reduction in Arc Flash Personal Protective Equipment (PPE) requirements.
Another benefit for alarm only HRG systems is the ability to locate faults while the equipment is still operating. Since the 60’s, pulsing ground fault detection systems have been a proven way of locating faults. Bender Series 2 and Series 3 HRG packages have optional RCMS490 12 channel ground-fault relays that can help automate the fault location and make it faster and safer for the electricians sent out to troubleshoot.
Conclusion
To improve power in mines:
- Implement portable load shock protection with HRG
- Utilize Bender NGR monitors on HRG and LRG systems to improve safety
- Consider adding the RCMS490 for automatic fault location
For more information about this application or to learn more about Bender technology related to your specific application, contact our team of experts.
This article is for informational purposes only. Bender provides the information "as is" without warranty and is not responsible for its accuracy or reliability. No warranties are given regarding its suitability for any specific circumstances.