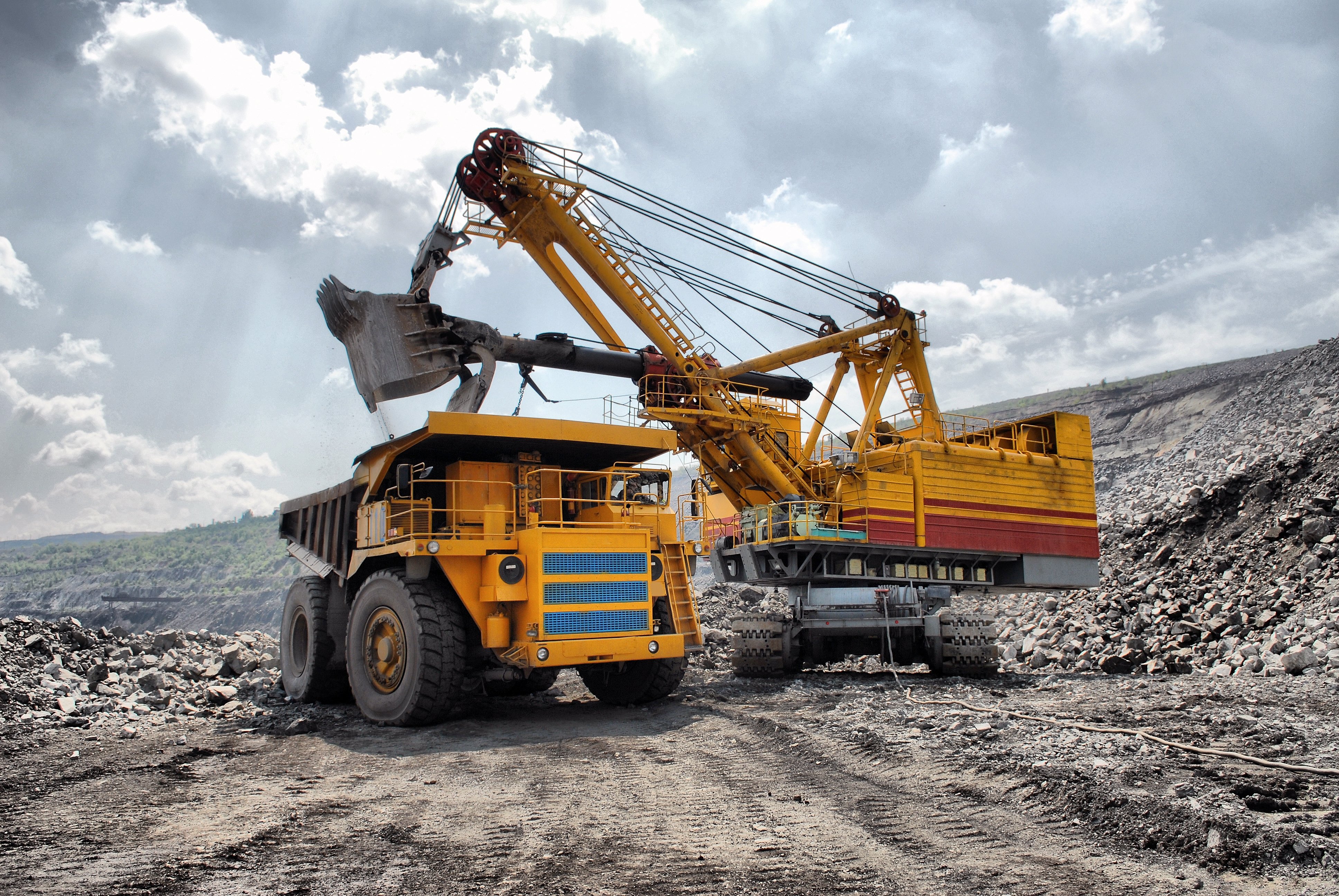
Mining is a demanding industry that is always in need of new and innovative products — especially those that can provide enhanced safety measures. These products must also meet quality standards to guarantee the continuity of operations under extreme conditions. One of the most challenging conditions is the altitude at which certain mines operate. There are mines in parts of the world that demand devices have the ability to work at tremendous heights — from approximately 2,000 to 5,000 meters (1.2 to 3.1 miles) above sea level.
The Andes mountain range are very rich in concentration of metals and minerals and have a rugged geography to add to the challenges. A large number of mining facilities can be found in countries such as Bolivia, Argentina, Peru, and Chile.
How does the operating height affect the performance of electrical equipment?
If you have ever climbed or traveled to high altitude locations, you may have experienced that as altitude increases, the body begins to feel changes and sensations such as labored breathing, headaches from lack of oxygen, and decreased temperatures. Air density decreases with altitude.
Air density not only affects people, but electrical equipment as well. If the equipment relies on air gap (separation of conductors via air as an insulating medium) or air cooling for operation they may face premature failure when used at altitude. There are fewer air molecules per unit of space, therefore dielectric strength and cooling capacity are reduced. Equipment designed for operation at lower altitude may not operate at some of the extremes seen in the Andes. At a minimum equipment must be de-rated.
Bender offers two modern grounding resistor monitoring solutions for the mining industry: the NGRM500 and NGRM700. The NGRM700 was the first unit launched and was designed to operate at altitudes up to 5000 m, allowing adequate space for increased air gap and better cooling at such altitudes.
These innovative products stand out because of their advanced ground-fault protection capability and accuracy in monitoring high resistance grounded systems. They are modern designs complete with communication capabilities: Modbus TCP (over Ethernet) and Modbus RTU (over RS-485). The fieldbus protocols are a part of our next-level Mining 4.0 and are the only ones in the mining industry to have an integrated webserver to manage settings, display measured values, and provide alarm notifications. Even local control and information is provided by an intuitive configuration using a graphical user interface with commissioning assistant.
By implementing Bender's NGRM500 and NGRM700 monitors, the main advantages are:
- Reduction of risk or electric shock with unique ability to detect ground faults across a wide frequency range (AC/DC faults)
- Enhanced system reliability and up-time with continuous monitoring of the system grounding
- Continuous system operation and online fault location in the condition of a first ground fault -in plant environments.
- Cost savings by allowing scheduled maintenance and avoiding emergency repair.
- Reduced risk of arc flash by up to 95% - when converting systems from solidly grounded to HRG.
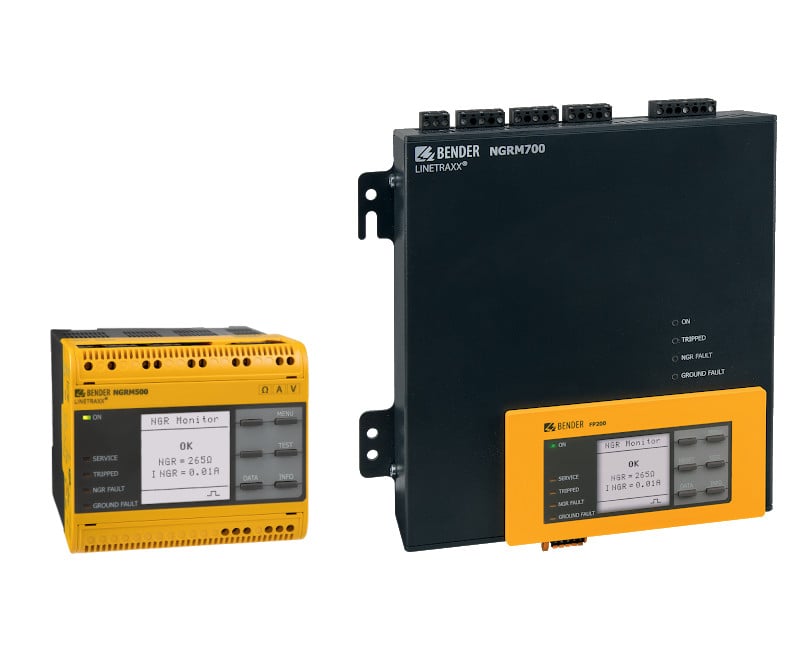
NGRM solution features
- Compatible with systems up to 25 kV
- Phase-Phase voltage (L-G)* and Neutral-Ground voltage V (N-PE) monitoring
- Continuous AC/DC NGR ground-fault monitoring
- Harmonic analysis of NGR current and voltage
- Active and passive measurement method, even when offline
- Operate up to 5000 m AMSL*
- Operating temperatures from -40C to + 70C
(*) Only the NGRM700 Version
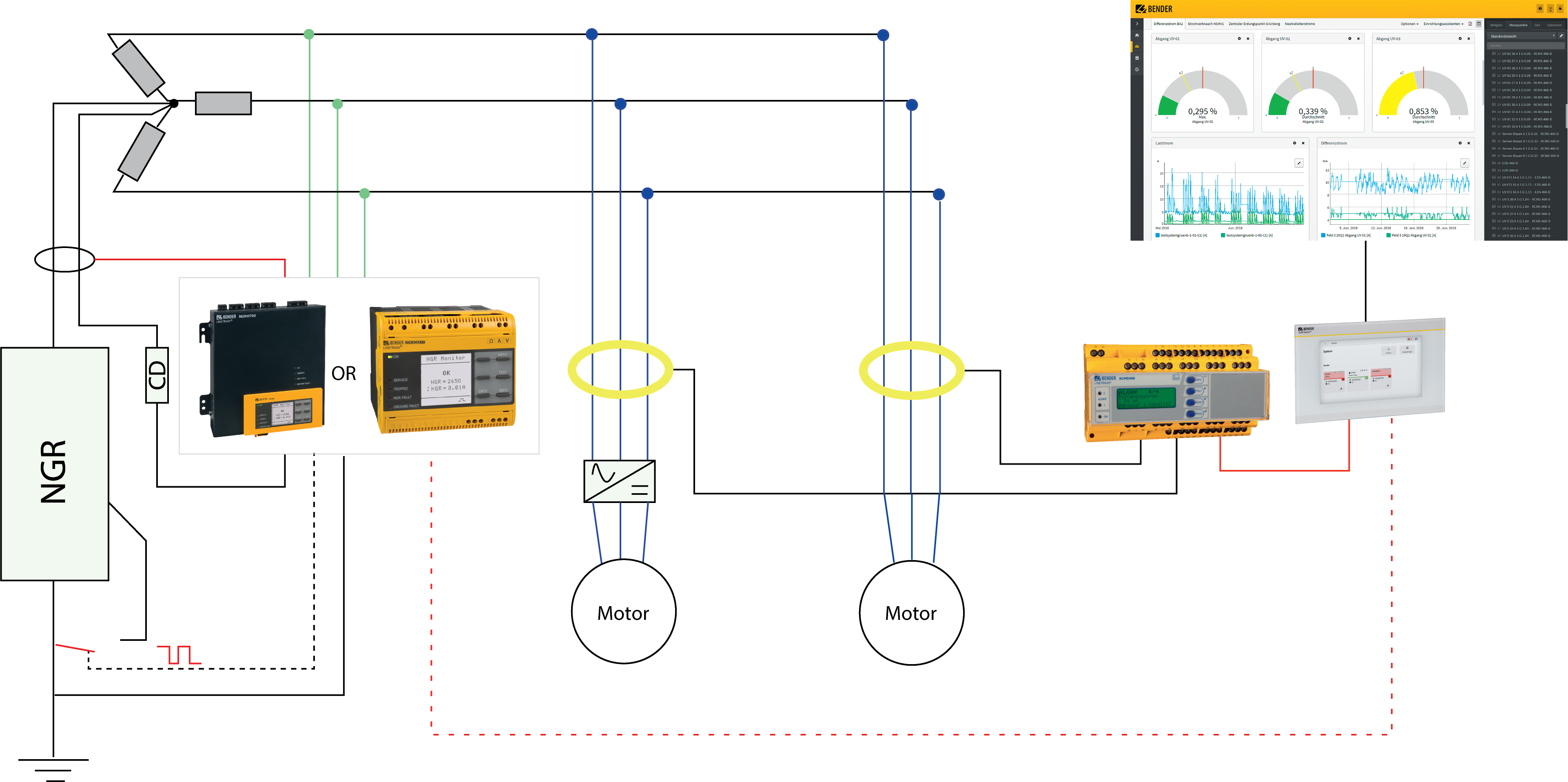
For more information about this application or to learn more about Bender technology related to your specific application, contact our team of experts.
This article is for informational purposes only. Bender provides the information "as is" without warranty and is not responsible for its accuracy or reliability. No warranties are given regarding its suitability for any specific circumstances.