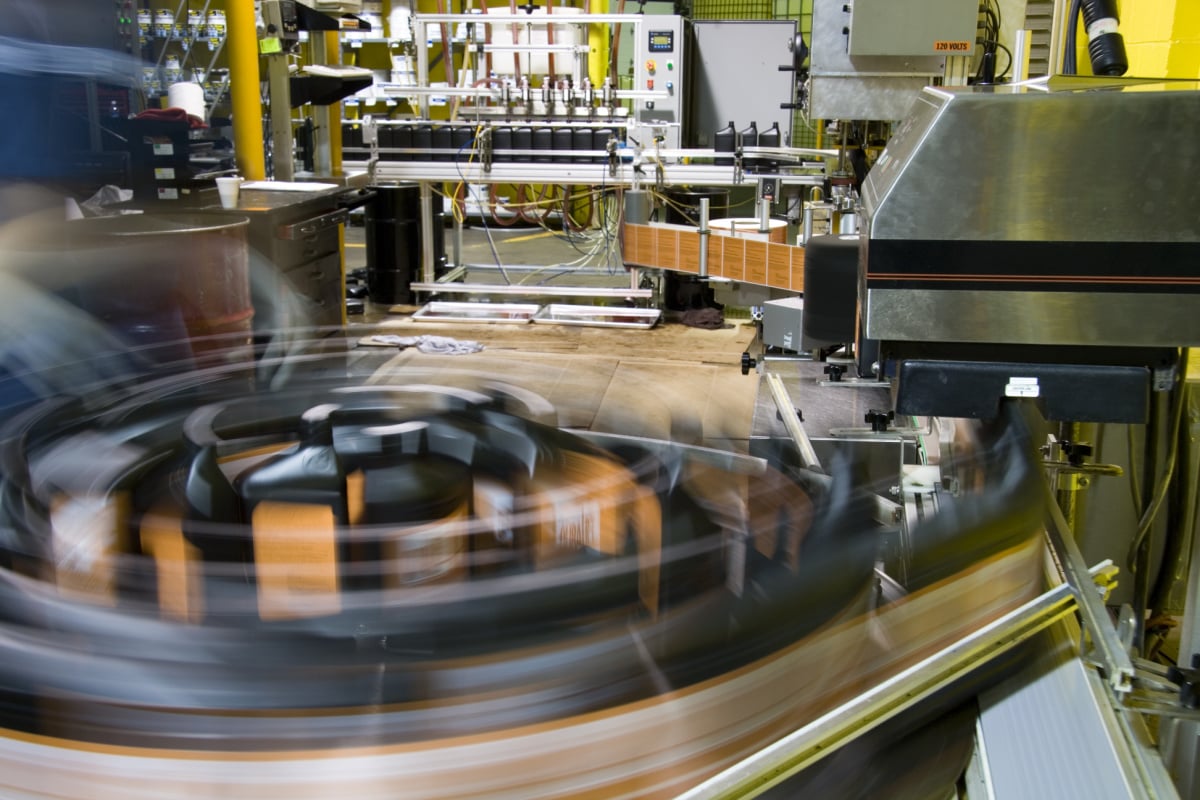
In 2016, Bender began offering NGR packaged solutions with a premium commissioning support option. Projects often face budget restrictions which cause a strong pushback to drop non-essential parts of a package. Bender has been successful in commissioning installations that previously had hit roadblocks and been unsuccessful in completing installation. Below are a few of the reasons and benefits of commissioning with Bender.
With the increasing digitalization of the workplace, it can be a challenge to know all products used at a manufacturing plant. A large off-road vehicle OEM specified Bender early on in their design stage. When it was time to install and commission, they hired Bender to finish the job. Bender devices were new to the customer, and commissioning support gave them comfort in product setup and operation.
As is common after construction, there were some original intermittent faults. Since our team commissioned the setup, our technical support had the benefit of knowing the relays were programmed properly, ensuring the focus could be spent on examining the downstream devices that were causing the faults. The customer was able to isolate and uncover a faulted HVAC unit and defective welder. This instilled great trust in the reliability of the RCMS490 and NGRM700s.
Bender Commissioning Process
The commissioning procedure for a Bender system involves several steps to ensure proper installation and functionality. On-site, a Bender representative assists in providing complete support with our package offering. Below is a general outline of the Bender commissioning procedure:
- On-site installation wiring verification/inspection
- Functional testing
- Calibration and configuration
- System integration
- Performance verification
- Documentation and training
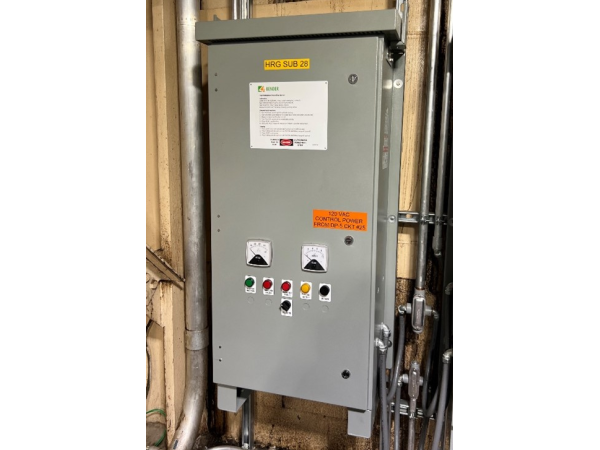
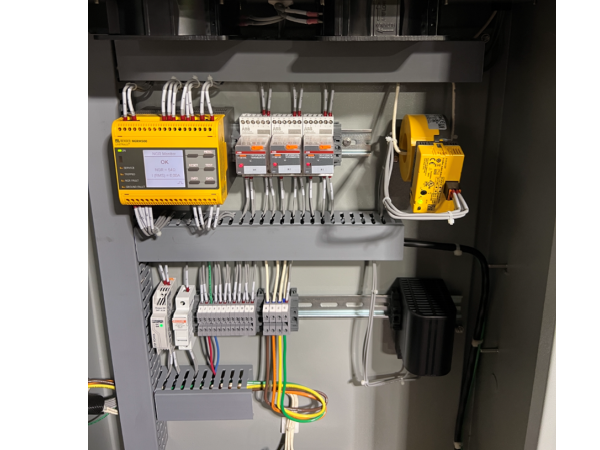
Dangers of improper installation or configuration
At the end of 2022, an industrial plant purchased a Bender grounding resistor with a 25 A let through current, zig zag transformer, and controls that included an NGRM700 NGR monitor. While commissioning support was offered, it was not purchased. The installation was completed and energized between Christmas and New Year's Day. Unfortunately, the unfamiliarity with the equipment and construction handoff resulted in some errors. The control package was never connected to the main breaker.
Similar to many other case studies involving equipment failure, there were two issues – a ground fault and an error during installation that could have been easily avoided with proper Bender commissioning steps. The fault propagated and since the plant protective devices were unable to disconnect, the time rating of the zig-zag transformer was exceeded, resulting in extensive damage and downtime for the plant. The resulting damage resulted in a three-phase fault that was cleared upstream by the utility, resulting in an unplanned outage for a small community.
It's important to note that the specific commissioning procedure may vary depending on the manufacturer's recommendations, the project requirements, and the type of Bender system being commissioned. It is always recommended to refer to the manufacturer's documentation and guidelines for detailed and accurate commissioning instructions
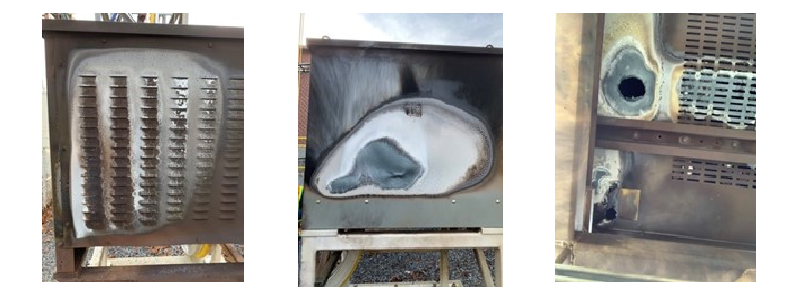
For more information about this application or to learn more about Bender technology related to your specific application, contact our team of experts.
This article is for informational purposes only. Bender provides the information "as is" without warranty and is not responsible for its accuracy or reliability. No warranties are given regarding its suitability for any specific circumstances.