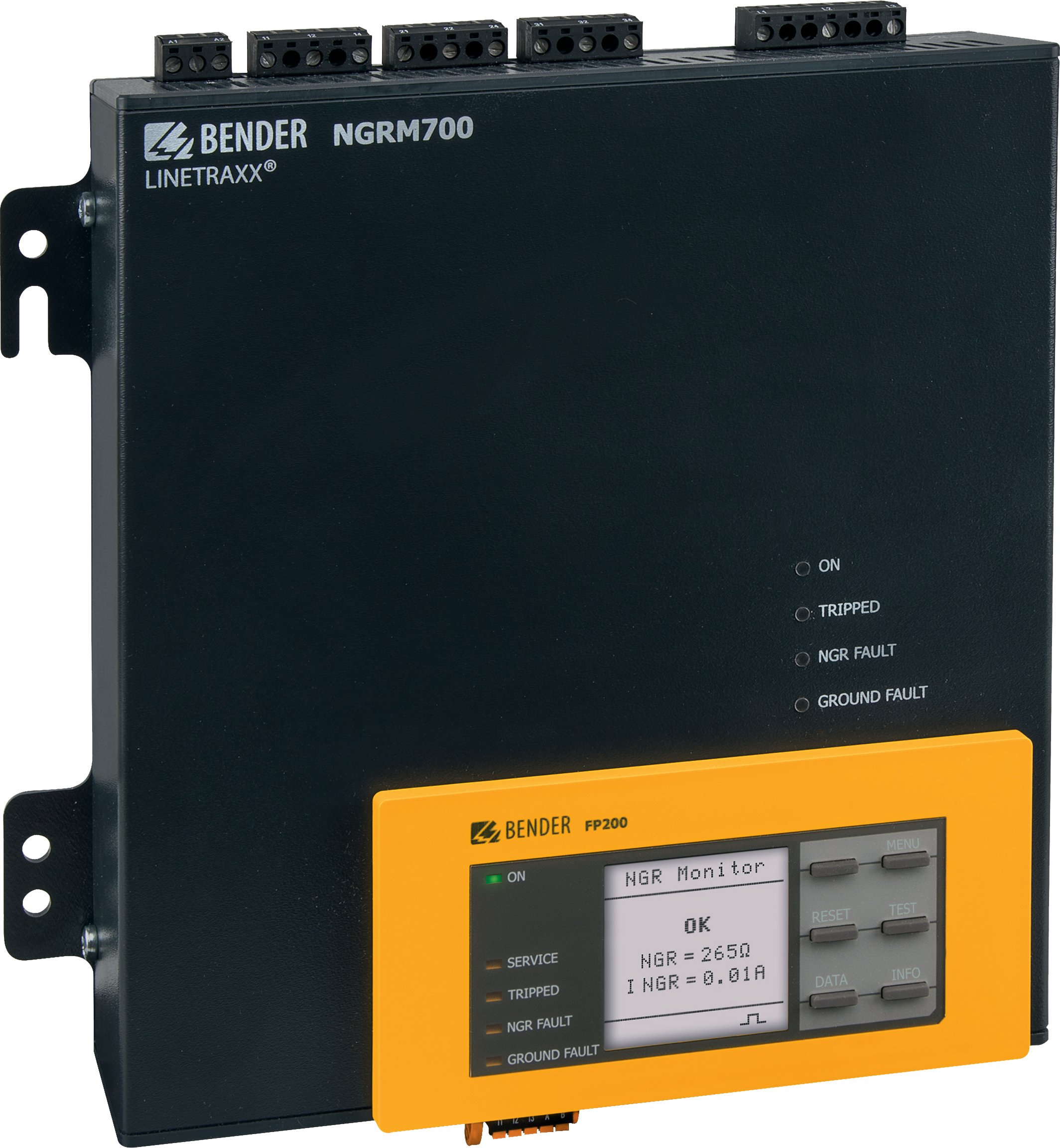
For decades, Bender has played a vital role in the mining industry in protecting equipment and personnel from electrical faults. Due to Bender’s historical success in mining applications, an end-user asked their consultant to design their system's ground fault protection with Bender to ensure they had a reliable and protected system.
Why Bender was Needed
In this instance, Bender worked directly with the consultant to review and analyze the overall system to identify the areas where the customer needed ground-fault protection to meet the mining code and ensure the best protection—starting from the main step-down transformer feeding the 600 V switchgear.
Bender worked with the consultant to confirm the charging current in the system to size the NGR appropriately for the HRG (high resistance grounded) system. After performing the charging current calculations and determining a very low charging current, the HRG system was designed with a 5A Bender NGR (neutral grounding resistor). The NGR contained an AC transformer and coupling device in the package connected to the Bender NGRM700. The NGRM700 was used to reliably monitor the health of the NGR with an active pulse for both the open NGR condition and a shorted NGR. This gave the customer peace of mind knowing they would be notified immediately of any failures and, therefore, avoid any severe equipment damage. This also ensured compliance with the Canadian Electrical Code regarding ground fault protection and NGR monitoring.
Getting Technical
The 600V switchgear had six main feeders going out to the MCCs in this electrical room. The client wanted Bender to take care of all the ground-fault protection for maximum reliability, and Bender also designed ground-fault protection at the feeder level. This was done by utilizing a single Bender RCMS (residual current monitor) multi-channel ground fault relay that can monitor up to 12 channels with one relay. This was important to capture low 1-2 A level faults and gave the OEM a minimal footprint in gear. The RCMS relay was combined with six Bender AC transformers since the loads were purely AC, and Bender AC/DC transformer technology was not required. With this solution at the feeder level, the customer can catch ground faults on the feeder level early. Since Bender technology was taking care of the feeder level ground fault protection, the consultant could use LSI breakers on the feeders and not require LSIG breakers, which reduced the overall cost for the end-user.
Like almost any mining application, the customer had a few receptacles using trailing cables to move equipment. For these receptacles, the consultant worked with Bender to design the Bender ground-fault ground check relay (RC48C) to monitor the ground conductor and ensure its integrity so the end-user can safely operate portable equipment. The RC48C will immediately cut power to the equipment if the ground conductor is shorted or breaks anywhere along the cable run to the equipment. This protection helps the customer meet the Canadian Mining Code for ground continuity monitoring of the trailing cable.
Bender's Solution: Above and Beyond
Lastly, the customer wanted to ensure that this data was captured and readily available. For this, the OEM was provided with a communications gateway that includes a 7” HMI (CP700) to centralize all of the data captured. This allowed the customer to access the relays' details and make any changes quickly. The gateway also will enable them to bring all this data to their third-party systems via Modbus TCP/IP communications and access it via the webserver. The CP700 was a priceless benefit for the customer to trend data and get notifications remotely, so no faults were missed, and any intermittent faults were much easier to troubleshoot.
The consultant was very appreciative of the support received from the Bender engineering team to help design the overall ground-fault protection for the salt mine and the support provided to all the other parties involved to ensure the entire process went smoothly. The end-user has had the equipment up and running without any problems and looks forward to working with Bender on future projects.
For more information about this application or to learn more about Bender technology related to your specific application, contact our team of experts.
This article is for informational purposes only. Bender provides the information "as is" without warranty and is not responsible for its accuracy or reliability. No warranties are given regarding its suitability for any specific circumstances.