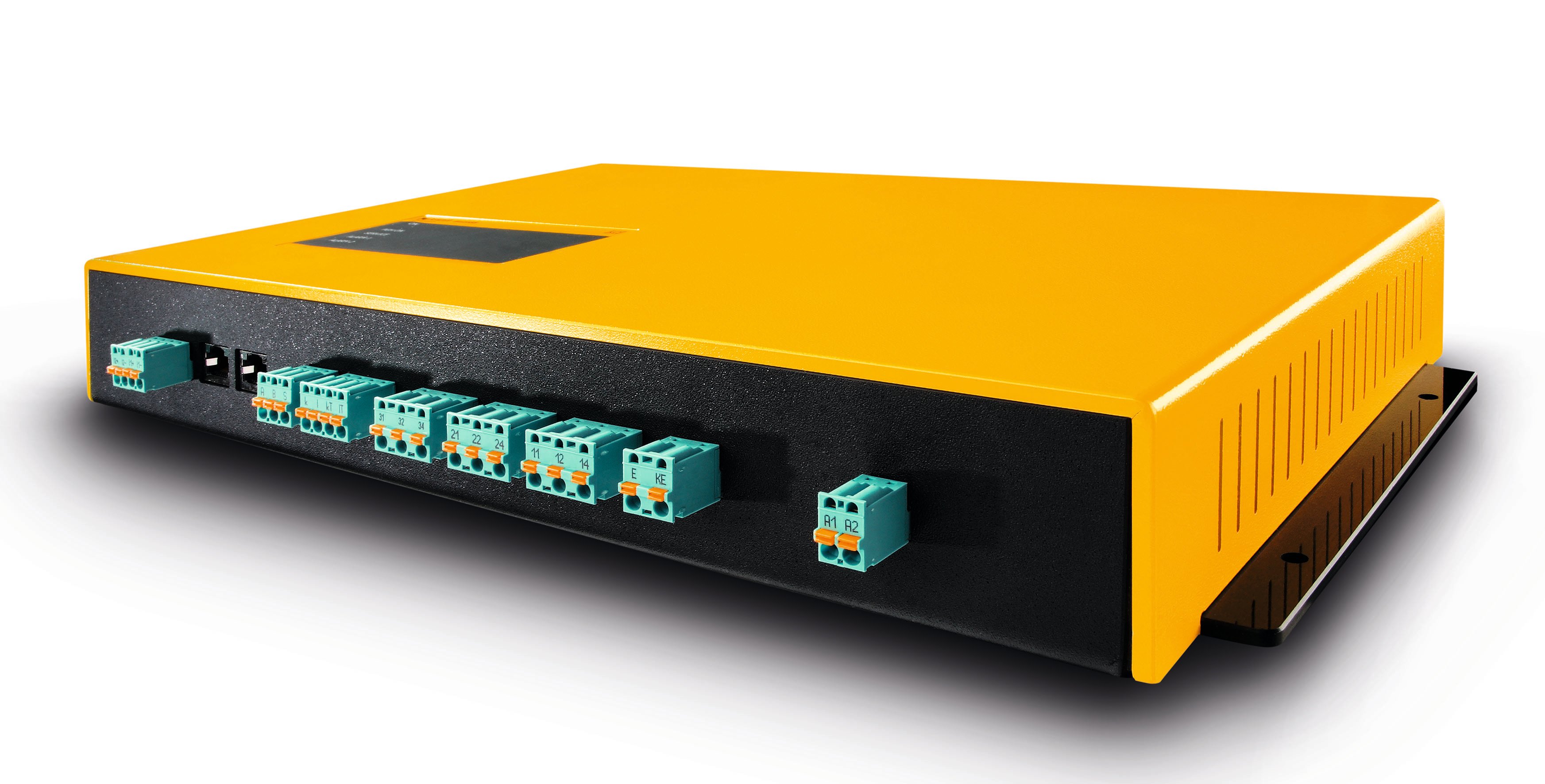
In recent years, Chile has become one of the largest renewable energy investors in the world. This is thanks to its high potential for power generation through solar resources (photovoltaic plants and concentrated solar power plants) and long coastlines with strong wind for wind power generation. Recently, this also became thanks to the ability to generate green hydrogen on a large scale by undertaking sustained promotion policies for the development and implementation of these technologies.
Why Chile?
With regard to the potential for solar energy generation, Chile has one of the locations with the highest solar radiation on the planet in a large part of its territory, extending over more than 40,540 square miles. This makes it extremely attractive for the construction of large photovoltaic parks, currently ranging from 50MW and 150MW for the smallest to 300MW for the largest; however, mega-plants of up to 400MW are already under construction.
Maintaining the productivity/performance ratio (PR) of the installations in accordance with the rates expected in the design of the projects is critical. Ensuring the safety of the installations against possible risks of fire due to insulation failures is of utmost importance. Fires can occur in different areas of the electrical systems of these power generating plants, such as: AC/DC cables, photovoltaic modules, junction boxes, inverters, and power transformers. These installations are often exposed to extremely severe environments* that cause degradation and accelerated aging over time.
*Factors that contribute to a severe environment:
- Extremely high pollution
- Saline environment
- Low or almost no rainfall
- Strong solar radiation
Which Bender products work best for PV plants?
In a large number of these PV plants, monitoring technology devices from Bender have been used to predict when the electrical system is no longer operating safely for the plant, the operators, and technicians. The advanced measuring method of the Bender ISOMETER® isoPV1685RTU/isoPV1685P, IsoPV with AGH has been specially developed for PV systems where slow voltage fluctuations (MPPT) are present during the day and night. These units are able to monitor the insulation resistance even in systems where extremely high system leakage capacitances against ground (<2000µF) are present, thanks to interference suppression methods. Adaptation to high system-related leakage capacitances also occurs automatically.
The embedded communications in the Bender insulation monitors allow the establishment of behavioral curves and trends of insulation deterioration, not only on a daily basis, but also seasonally (depending on the season of the year). This provides the basis for studies and analyses of traceability and trends in order to make the best decision to intervene in the systems when required, before an unscheduled failure and service interruption is generated.
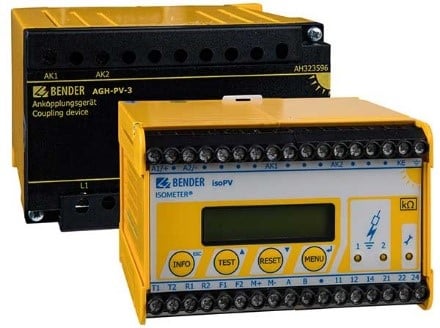
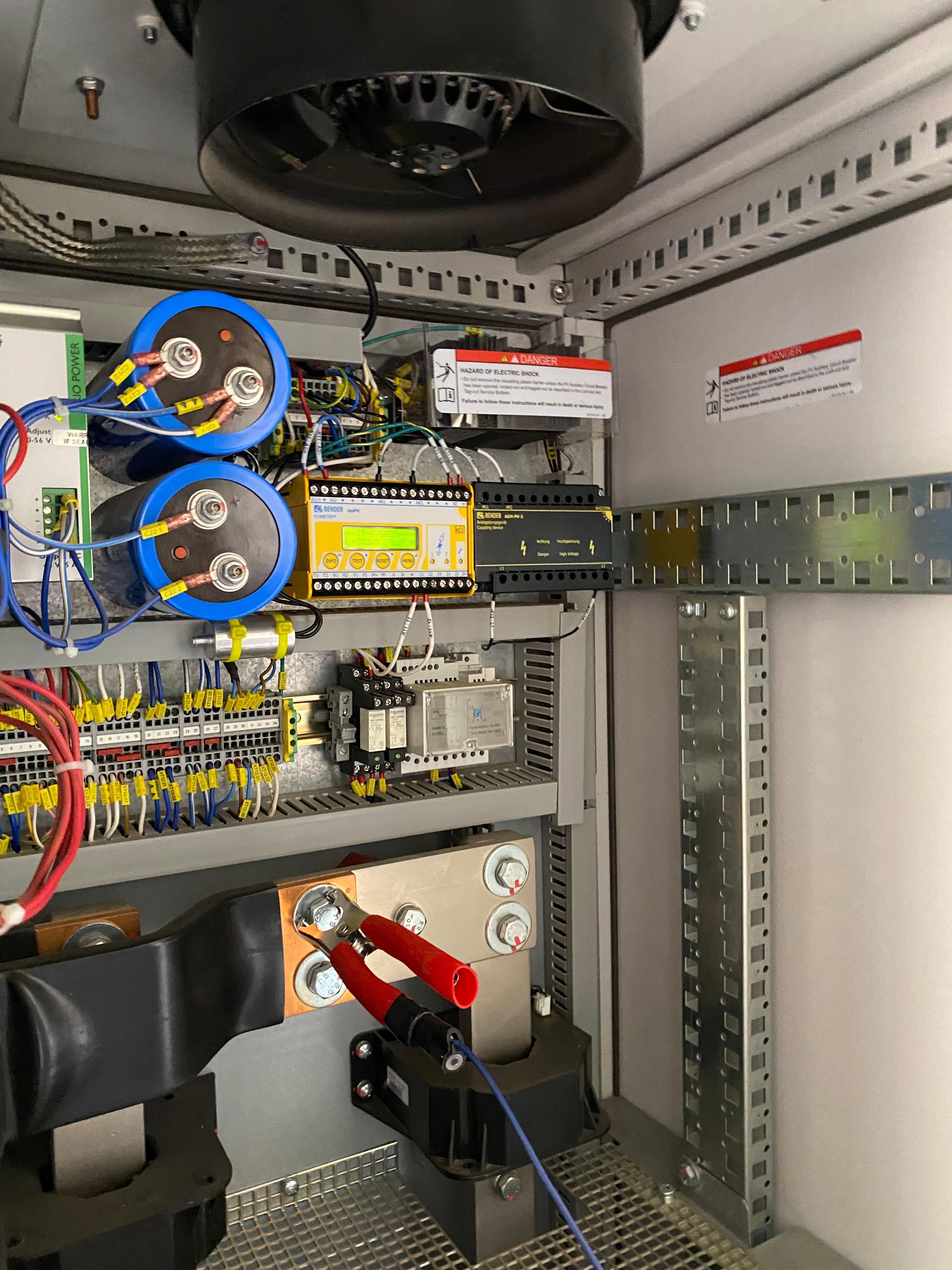
Operators and managers of large photovoltaic plants face two daily challenges: keeping the installation at the highest PR possible, and achieving the least possible impact on the grid in the event of an alarm due to an insulation fault. To succeed, am effective tool is the ISOSCAN® EDS3096PV portable fault locator. This device allows the user to detect both the main output string circuit of the affected inverter, the secondary string downstream of the combiner box, and the particular component that generated the fault condition within that circuit. With this device, fault location can be done fairly quickly (typically a few hours) and does not involve disconnecting the system for fault location, thus not affecting power generation.
For more information about this application or to learn more about Bender technology related to your specific application, contact our team of experts.
This article is for informational purposes only. Bender provides the information "as is" without warranty and is not responsible for its accuracy or reliability. No warranties are given regarding its suitability for any specific circumstances.