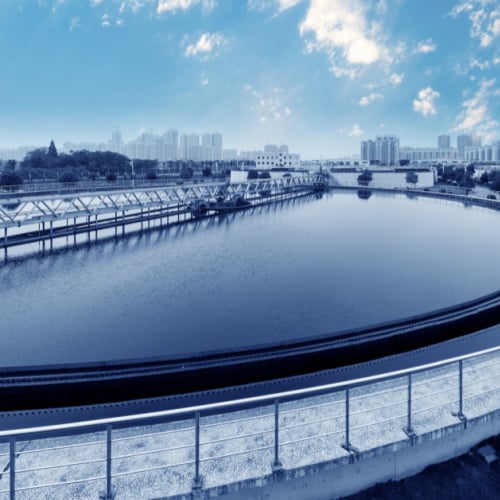
Since the late 19th century, sewage has been cleaned through chemical and physical processes so most pollutants are removed before the water is released into streams, rivers, and the ocean. Over the years, an increase in public concern for environmental quality led to more stringent regulation of wastewater disposal practices. Wastewater treatment plants have become larger and more complex, requiring more electricity to accomplish their tasks. Bender's simple solutions are able to monitor the electricity used at these plants, preventing lost time due to ground faults.
Old equipment needed a replacement
Bender was contacted by two consultants working on two large Wastewater Treatment Plants (WWTP) to upgrade and design a complete ground-fault protection system. While both were wastewater facilities, their problems were vastly different and required different solutions by Bender.
The first plant - RFB700
In the first WWTP, it was discovered that the facility had existing ground fault protection, but it was much older technology. They wanted to update their systems to maximize their operational availability while making the protection system smarter. The system grounding arrangement was high-resistance grounded and the main problem the customer was facing was a lack of operational availability on the second ground fault. The ground fault system they had did not have reliable prioritization to trip the lowest priority feeder in the event of a second phase-to-ground fault. Due to this, when a second ground fault did occur, the main breaker would trip the entire system and they would lose every feeder instead of just the lowest priority feeder.
Bender offered the customer the RFB700 retrofit kit that is designed to easily slot into the existing racks for a seamless upgrade without causing any major changes to the plant. The Bender RFB700 kit included secondary ground fault protection for up to 12 feeders per rack and had the ability to monitor up to 120 feeders. This allowed configurable priority settings by the customer for the feeders to only trip the lowest priority feeder in the event of a second ground fault to go back to first fault conditions, without losing power to the entire plant. This is an unquantifiable benefit for the end user as this critical facility could not afford to have nuisance trips that interrupted the entire operation. The kit also included an NGRM (Neutral Grounding Resistor Monitor) to actively monitor the health of the customers HRG systems, as well as bring them up to CEC 2021-Section 10 requirements. All data gathered by the RFB700 kit communicates through MODBUS TCP/IP to the customer's system as per the customer's requirements to make the system smarter and have all captured data centralized.
The second plant - NGRM500
The second plant was a new WWTP and the customer required assistance designing the resistance-grounded system for high-, medium-, and low-voltage systems. The end user had past issues with ground fault equipment not being able to detect both AC/DC ground faults. The equipment at the other plants only detected an AC ground fault at the fundamental frequency, so any DC ground faults as well as low-frequency AC ground faults flow through the system undetected. These faults continue to develop and eventually cause serious damage to equipment, specifically their variable frequency drives (VFDs). The Bender team worked with the consultant to perform the capacitive charging current calculations to appropriately size all the NGRs; specifically, for the 12.47kV Transformers, HRG systems for the emergency generators as well as the Zig-Zag transformer and LRG system grounding the Bus when the system is fed by the emergency generators. All the NGR systems were designed with the NGRM500 to detect both AC and DC ground faults on the system and monitor the health of the NGR as specified in 2021 CEC- Section 10.
Additionally, to protect all of the feeders, two Bender multi-channel ground fault relays were required to protect up to 24 feeders inside each MCC (Motor Control Center). These protection relays come in a compact form factor and are combined with AC/DC CTs to protect all the large drives in the plant. They detect any DC faults at 0Hz as well as low-frequency AC faults occurring inside and after the VFD, while providing a complete harmonic analysis of the measured currents. This is vital for the end user to be able to detect any types of AC and DC faults early to avoid any damage to the drive that they have seen in their other plants that only have rudimentary ground-fault protection. It will result in them reducing operational costs and downtime when having to service these drives on their existing plants.
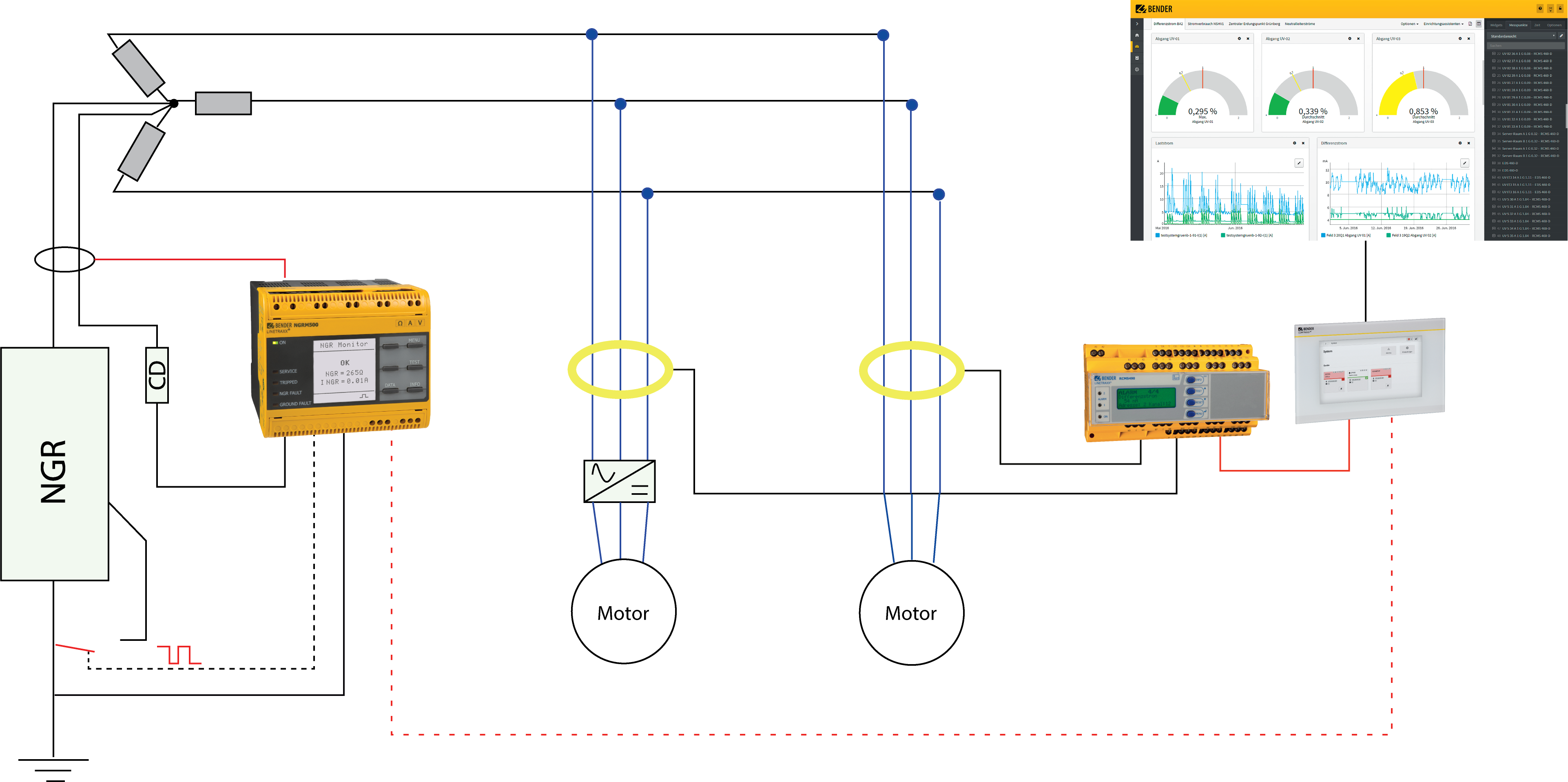
Conclusion
Water and wastewater facilities must operate reliably and safely, which is why Bender has developed solutions suitable for practically any resistance-grounded electrical system within the facility. Both consultants were very happy with Bender's support on the design suggestions and the benefits Bender technology provides the end user. Bender's RCM and NGRM products provide this advanced level of protection and can be included in turnkey HRG packages. Bender's solutions continue to provide priceless value to the end user by providing them with state-of-the-art technology and with tremendous project support to ensure their critical facilities can operate efficiently with reliable ground-fault protection systems.
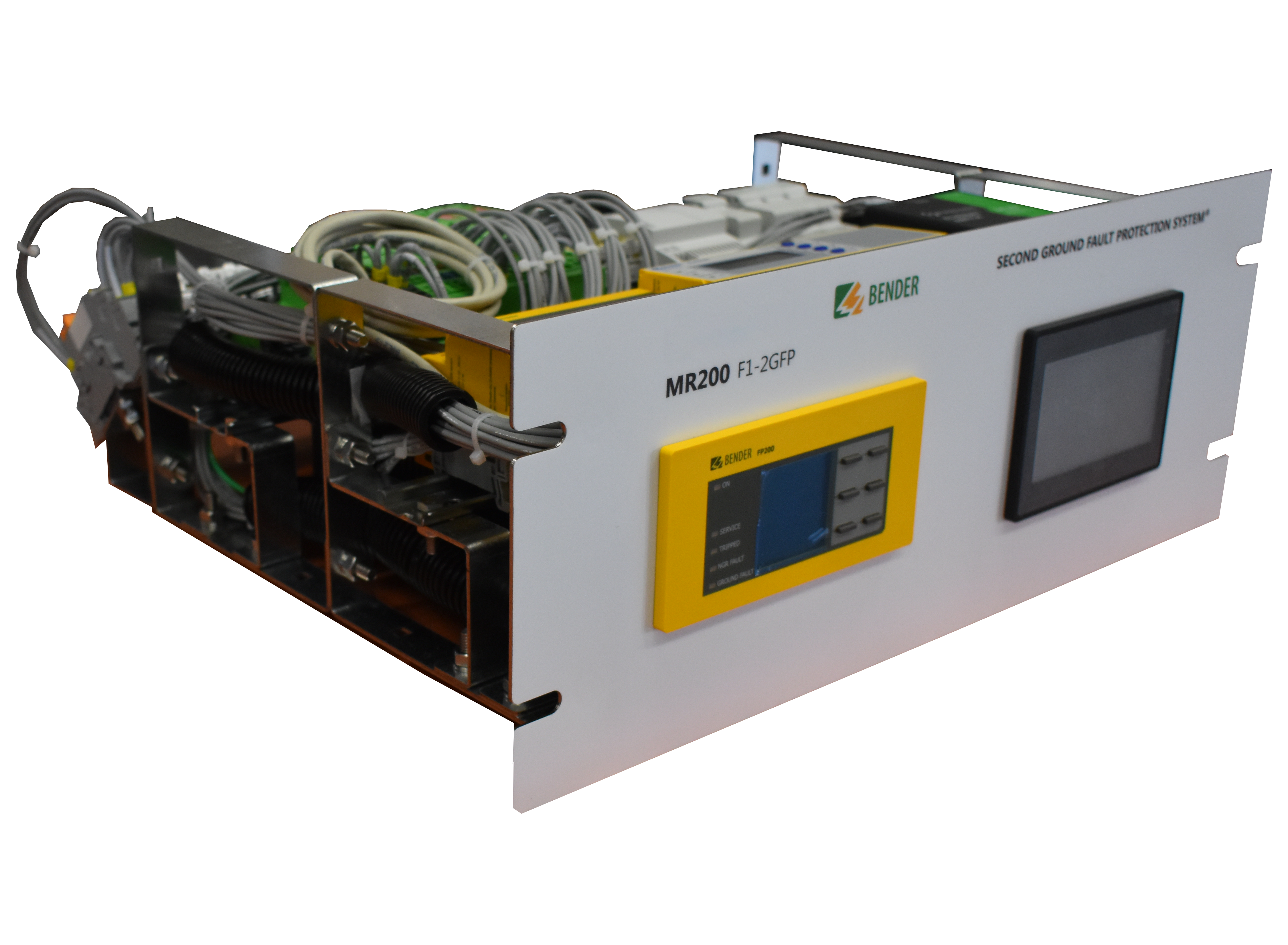
For more information about this application or to learn more about Bender technology related to your specific application, contact our team of experts.
This article is for informational purposes only. Bender provides the information "as is" without warranty and is not responsible for its accuracy or reliability. No warranties are given regarding its suitability for any specific circumstances.